Can the Fly Ash, Metakaolin and Silica Flour in Light-Wellbore Cement Slurries Prevent Alkali-Silica Reactivity of Glass Microspheres?
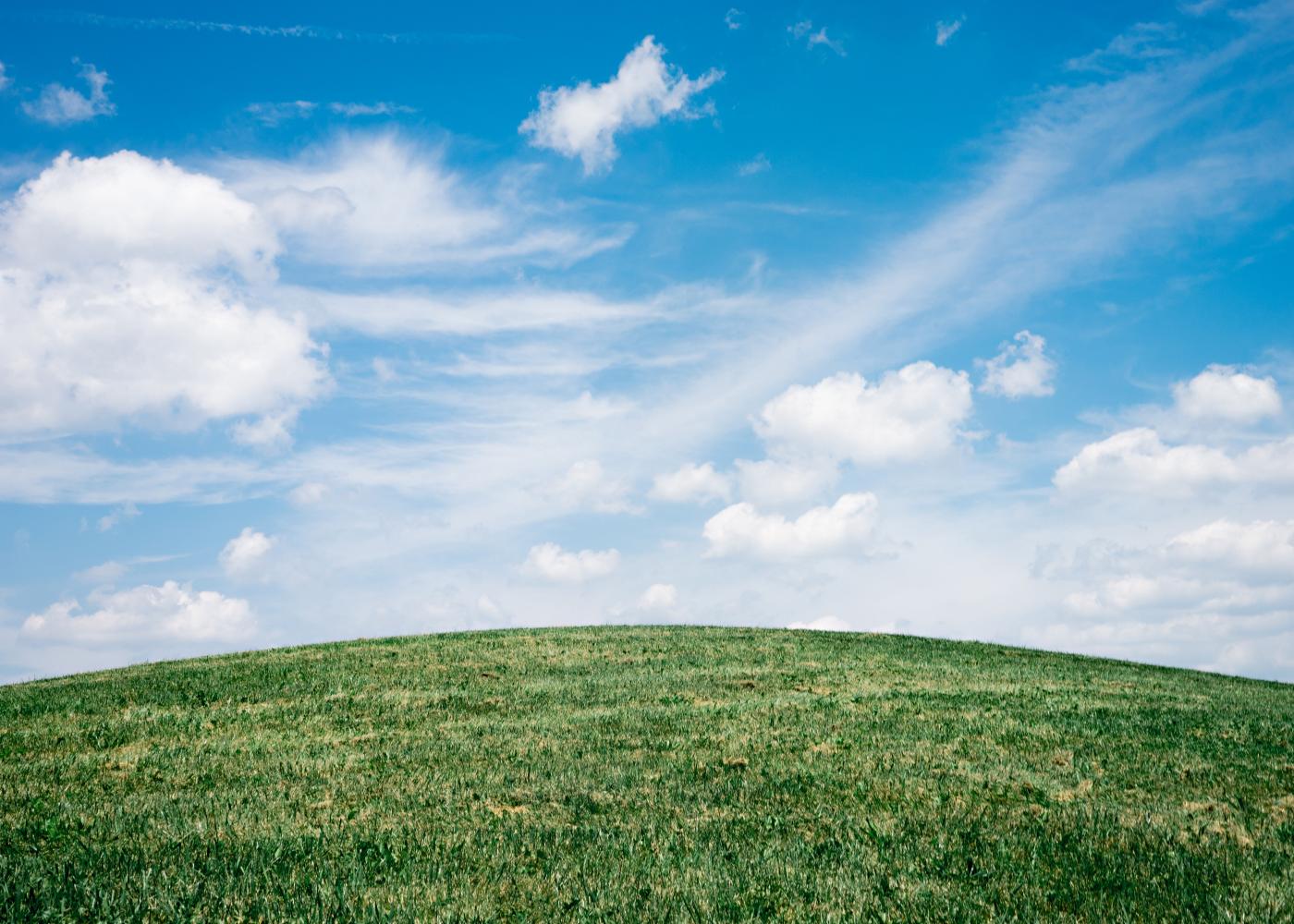
Cementing is a required process for drilling and completing any types of wellbores, those producing geo-fluids, or used for injection of waste fluids. The cementing process is completed by pumping the cement down through a casing string, then back up between the formation and casing where the cement forms bonds between the two and seals off fluid flow in this area. The hydrated cement slurries used in the wellbore construction are expected to maintain their integrity throughout the life span of the well, often at high temperatures and pressures as well as being exposed to geochemically aggressive fluids. Loss in cement integrity can lead to fluid migration through the cement, as well as structural issues that result in costly workovers during service life of the well, and would increase complexity of permanent plugging and abandonment of the well as well. Such failures result in HSE accidents that impact society and cause economic loss to the industry. Geothermal wellbores require durable materials and special cement, such as geopolymers. Aluminate-based cement have been investigated and redesigned to the same degree as Portland Cement. [1],[2]
In the geothermal reservoirs, the subsurface environment is associated with high T. In order to prevent cement mineralogical changes known to cause strength retrogression and low structural integrity of cement sheath, various Si-rich materials have been reported as a solution in mitigating strength retrogression. Wellbore integrity issues and potential wellbore cement failure, which becomes an issue if the well cannot maintain its structural integrity as well as the zonal isolation, can potentially allow for uncontrolled and undesired fluid migration. Prevention of this phenomena, which requires the use of silica-rich additives, is normally achieved by the addition of silica flour in regular and heavy weight cement slurry (density above 13ppg). However, for light cement slurries (bellow 13ppg) that can be achieved with glass microspheres, which are not crystalline in nature and are susceptible to Alkali-Silica Reactivity (ASR). Glass fiber can also be a source of ASR, as it can be used to increase fracture toughness of cement. [3],[4]
Lightweight cements can be achieved through a variety of different approaches. The first and easiest is to increase the water ratio of the cement, although this method can only be used until the cement slurry reaches a density of 1.55g/cm, after which the cured cement will no longer be able to provide the necessary integrity of cement. To achieve densities below this value, two main methods can be used. The first method is foaming the cement, where nitrogen gas is mixed into the cement, replacing a portion of the bulk cement and effectively lowering the density. This method can have instability concerns due to the coalescence of nitrogen bubbles forming large channels in the cement, allowing for fluid migration. [5] The other method is to mix silica-based microspheres into the cement, which have low specific gravities and will lower the density. However, these microspheres have been shown to lead to alkali-silica reaction (ASR) in the cement. This is due to the high salinity pore fluids reacting with the microspheres, forming expansive ASR gel that can lead to loss of structural properties of the cement as it expands as well as cracks. [6],[7]
ASR has long been studied in cement and concrete research and a variety of methods have been shown to help in the prevention of ASR. These methods typically involve mixing some chemical into the cement that will react with the hydroxides early on so that they are not present in the pore fluid latter to react and break apart the silica content. Different temperatures and silica composition and salinity of the environment are among the conditions that affect ASR. [15]
Additionally, recent studies have shown that confining pressures to control ASR expansion with increasing pressure leads to less expansion [18]. Also seen in Lingard, et al., 2016 [18] was that ASR will expand more in the direction of less stress. In the wellbore, that would mean that more care would need to be taken in understanding how the forces would act on the cement.
Conventionally, this is done by adding pozzolanic materials such as fly ash or slag to prevent ASR. [8],[9] Additionally, lithium compounds have been shown to achieve ASR prevention as well. [10],[11] Metakaolin is another compound that has been shown to effectively work as a pozzolanic material for preventing ASR and leading to higher strength development, as well as lower pore space in the cement. [12],[13] This study looks at and compares the effects that fly ash (FA) and metakaolin (MK) have on lightweight wellbore cements containing silica-based microspheres as ASR prevention.
The materials used for this study include Haliburton class H cement, 3M HGS19K46 microspheres with a nominal density of 0.46 g/cc, an average diameter of 20 microns (Figure 1 and Figure 2), with survival pressures of up to 19,000 psi. The Fly ash is class F from Halliburton and Metakaolin is from PowerPozz Advanced Cement Technologies.
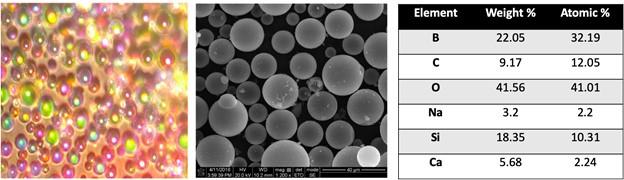
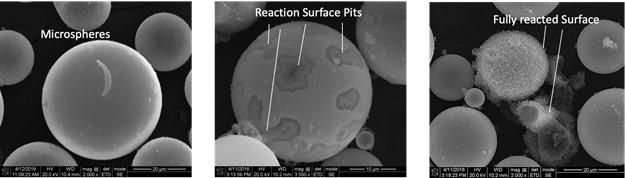
Research showed that metakaolin works in lower mixed percentages than fly ash. Therefore, this reasoning was implemented to justify the mix percentages of fly ash and metakaolin. The samples were prepared with different percentages (see Table 1) of fly ash and metakaolin to investigate the effects of additives on the cement after one month, compared to samples that didn’t have preventative additives. Bentonite was also added to prevent solid separation, 2% woc (weight of cement). All samples were made at average density of 1.55 g/cm3 to test a consistent weight that could be used for the same cement slurry design. Mix proportions for both MK and FA can be seen in Table 1.
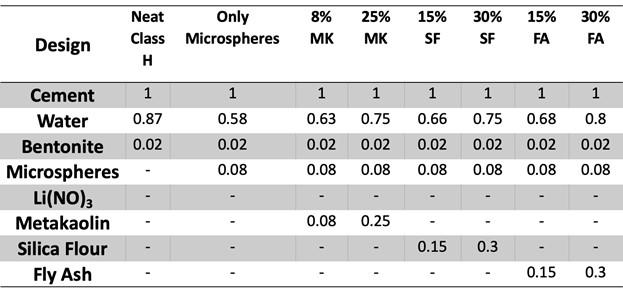
Samples were mixed in a Waring laboratory blender in accordance with API 10B recommended practices. Bentonite was pre-hydrated at approximately 16,000 RPM for five minutes. After this time all other solids were mixed in, except the microspheres, at 20,000 RPM for 35 seconds. After this time microspheres were mixed in by hand with a spatula until evenly distributed. After being mixed, samples were poured in 7.63x2.54 cm cylindrical brass molds. The samples were kept in the molds for 24 hours at room temperate in order to set and then moved to a closed container containing a solution of calcium hydroxide and deionized water, at pH 13. These containers were placed in the ESPEC environmental chamber at 700C and 100% relative humidity for 28 days.
After this time, samples were removed from the chamber and prepared for a series of different testing (Figure 3 and Figure 4). The first property that was tested was porosity. To do this, samples were cut on both ends to a length of 5 cm. The samples were then soaked in acetone for 24 hours to replace the pore fluid and minimized precipitants formed during drying. Next, the samples were left in an oven at 600C for 24 hours, after which the temperature was increased to 1050C to completely dry the sample. After this time porosity was determined using Core Labs UGV-200 UltraGrain Volume helium porosimeter.
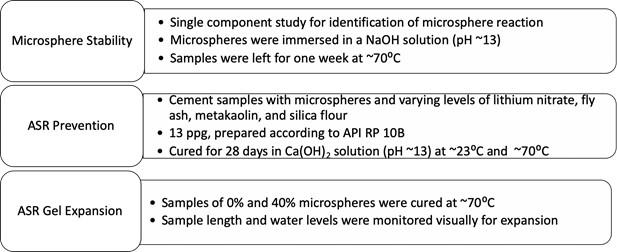
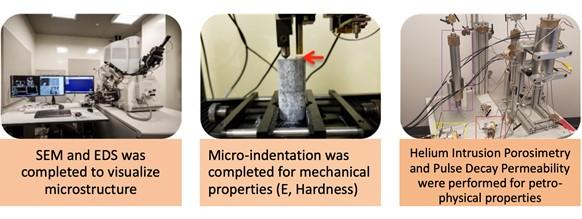
Knowing the value of porosity, the value for permeability was determined using the Core Labs Pulse Decay Permeameter for brine/water. In this test, the non-dried cement cores are placed in a rubber sleeve inside a high-pressure container. The container has a pressure of 34.5 MPa, then deionized water is used to move across the core. The entire core system is brought to 2.76 MPa, then one end is raised to 3.45 MPa and the pressure difference across the core is recorded with time. Using this pressure change as well as material and fluids properties, a line is created with the slope of the line giving the permeability.
Mechanical properties of the cement were also tested on samples that had not been dried. Micro-hardness was tested using a Nanovea Micro/Nano Module. This device applies a force onto the sample using a micro-hardness Vickers diamond tip and measures displacement of the tip as the load is applied to create a depth-versus-load curve. This curve is then used to calculate hardness and Young’s modulus during the unloading portion of the curve.
Finally, to visualize the effects that the different additives had on the cement, Scanning Electron Microscopy (SEM) was conducted. A dual beam-focused ion beam microscopy, FEI Quanta 3D FEG/SEM was used to do imaging in Secondary Electron (SEI) and Backscattered Electron (BSE) mode. Samples were dried by the same method as those used for porosity. Then samples were polished down to a 1 micron finish, using a series of polishing pads and placing the samples in an ultrasonic bath between each pad. After polishing, the samples were coated with a conductive carbon coating to prevent charging effects. Imaging was done at 10-20 KV and 27 pA.
The impact of glass microspheres on the petrophysical properties is presented first, as these are parameters which define whether wellbore cement provides zonal isolation (Figure 5 and 6). This if followe by the micromechanical properties, which relate to mechanical integrity of the wellbore cement, and the level of elasticity, often not present in a heavy weighthydrtaed portland cement slurries (Figure 7). Both of these sets of results can be further explained by microstructural characterization, and several micrographs shown in Figures 7-11 testify to this effect.
Figure 5, Figure 6, and Table 2 show the results from the porosity, permeability, and indentation tests obtained on cement samples with and without MK and FA. Values shown are averages of 3 samples tested with ± showing standard deviations. In case of porosity and permeability, up to 3 measurements were obtained from each sample, and in the case of indentation, 6-12 measurements were obtained per sample in order to reduce the error as a result of cement heterogeneity. Following these trends, conclusions can be made about the mechanical and petrophysical properties of these cements. All samples tested were Wellbore cement slurry Class H, 13ppg, tested at 1x2-inch core after 28 days hydration cured at 700C.
From the petrophysical point of view (Figure 5 and Figure 6), additions of fly ash and metakaolin decreases the porosity of the cement with higher additions of fly ash having a larger impact on porosity as compared to the high additions of metakaolin. These trends with porosity are also counted into permeability with the additives lowering permeability and metakaolin having a larger impact. These results match with those that have been seen in other studies like Shen [12] and Moser [13]. Shen showed that at higher levels of metakaolin, ASR effects were less and accompanied by larger reductions in porosity, with optimal MK levels being around 10%. Moser showed that metakaolin was more effective at preventing ASR than fly ash because of lower permeability. These decreases in porosities and permeabilities are due to the pozzolanic reactions of curing in the cement. As these reactions occur more, calcium silica hydrate (C-S-H) is formed. This additional C-S-H closes pore spaces inside the cement as well as adding to the cement strength.
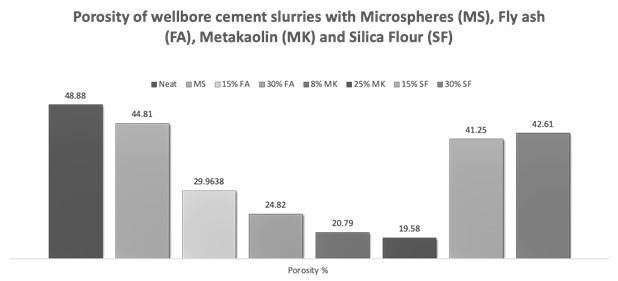
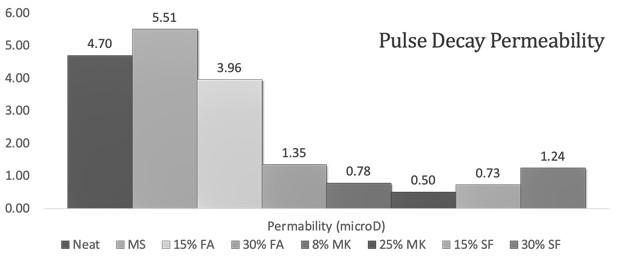
Mechanical property changes (Table 2) are shown to follow different trends than those seen in the petrophysical properties. With hardness at low levels of additions of both fly ash and metakaolin, not much changes when compared to no additions, but hardness increases at high levels of additives. This trend shows that with higher levels of addition, more pozzolanic materials will create more C-S-H and increase strength. Young’s modulus has a similar trend
with low levels of additive not having large changes compared to cement with no additions. But at high levels, fly ash and metakaolin act differently; fly ash increases Young’s modulus while metakaolin decreases the Young’s modulus. Therefore, it can be concluded that metakaolin is making the cement more elastic while fly ash results in more brittle material. This means that metakaolin would be a more desirable material to use in an environment with changing stresses. These changes also mirror the changes seen in previous studies like Shen’s [12] where metakaolin additions resulted in approximately 35% compressive strength addition, which is almost the same value seen in this study.
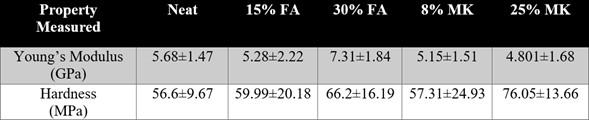
The image-based investigation was used to visualize the effects these additives had on ASR development. These scanning electron micrographs provide good insight into internal structure and arrangement of various phases present in hydrated cement, with and without MK and FA. The spatial distribution of pores and microfractures is another useful insight that microscopy provides in terms of material characterization. Figure 7 shows micrographs at two different magnifications in order to depict a more global view (low mag) and a more detailed view (high mag). Figure 7 shows a microsphere in the cement slurry containing no ASR preventing materials. In this image, the microsphere wall is completely reacted, leaving nothing but an ASR and C-S-H gel where the wall once was. The addition of MK, shown in Figure 8, provides evidence that there is no reaction at the microsphere wall. The same impact was observed when FA is used (Figure 9). That the microspheres are not impacted by ASR, and that there is no trace of silica gel, show the prevention mechanisms is effective.
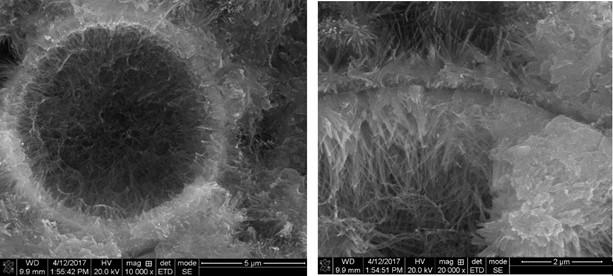
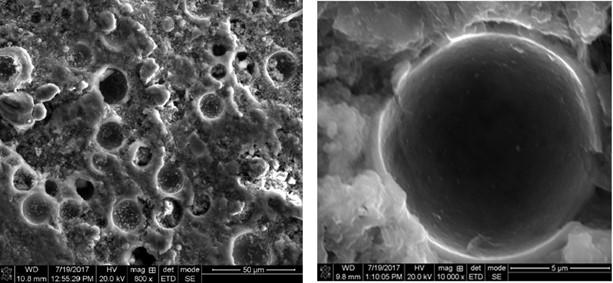
These visual observations corroborate with the data from the mechanical and petrophysical properties shown in Table 2. We can report the effectiveness of both metakaolin and fly ash as ASR preventing additives in lightweight wellbore cement slurries when glass-based microspheres were used, and at percentage replacements shown in Table 1. It is important to state that the ASR prevention was not achieved at the expense of petrophysical and mechanical properties, which might be different at different densities of cement slurries and at a different percentage of MK and FA used.
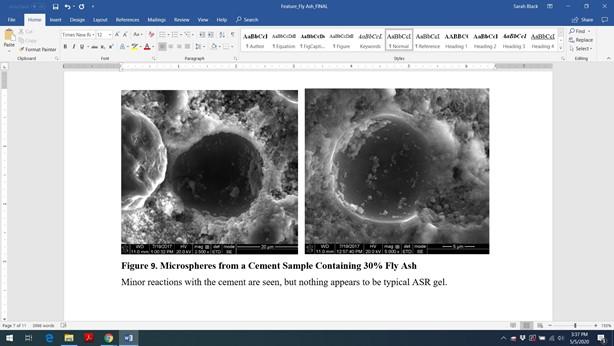
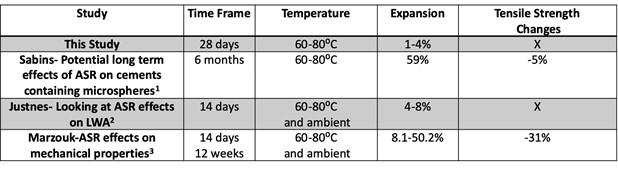
Wellbore integrity is critical to the lifecycle of every drilled well and determines if a well is able to stand up to the changing pressures and temperatures produced throughout its lifespan, until it finally gets to the plug and abandonment stage when it has to be able to stay intact for the rest of time. Having a cement sheath to maintain the structural and petrophysical integrity throughout all of this is essential. For example, in the Gulf of Mexico, where lightweight cement is used to complete wellbores in unconsolidated and depleted formations, this is not the case as 43% of 15,500 wells drilled have reported integrity issues. [14] The use of microspheres has the potential to lower the percentage of wellbore integrity issues by not allowing channels of gas to form like with foaming, but ASR must be controlled. ASR can be triggered by different types of amorphous Si-rich materials, but the environment in which the cement is cured has a vast effect on ASR formation.
This study reinforces the effectiveness of using fly ash and metakaolin to prevent ASR and also strengthen cement while lowering permeabilities. This is done through the pozzolanic reactions, and both of these materials lead to the onset that creates additional C-S-H. [17] Both are mostly amorphous silica that will react like cement and form C-S-H, but metakaolin is around 40% aluminum oxide, whereas fly ash has around 15% aluminum oxide. The SEM micrographs in Figure 10 shows very clearly the negative impact of high alkalinity pore water of Portland cement on the chemical stability of glass microspheres. Even though these types of materials have good testing performance in terms of mechanical stability where they clearly outperform foam bubbles, their long term stability might cause problems at a later date.
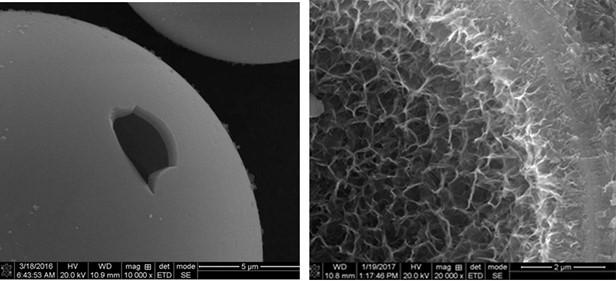
The use of microspheres has the potential to lower this percentage by not allowing channels of gas to form like with foaming, but ASR must be controlled. ASR can be triggred by many types of silica additions but the environment in which the cement is cured has a vast effect on ASR formation.
This study showed how metakaolin and fly ash can prevent ASR in lightweight wellbore cements containing silica-based microspheres as well as the impact each had on mechanical and petrophysical properties of the cement. This ASR prevention can be seen visually under the SEM.
Both metakaolin and fly ash lower porosity and permeability with higher mix percentages, having larger impacts on both values. Metakaolin addition results to both lower porosities and permeabilities than fly ash with less addition.
Hardness increases with the addition of fly ash and metakaolin, with metakaolin having a larger impact on hardness than fly ash.
Young’s modulus was not affected by additions of these supplemental cementitious materials in small percentages but at high percentages, different effects are seen. Fly ash increases Young’s modulus while metakaolin decreases Young’s modules.
Because of metakaolin’s ability to prevent ASR at lower mix percentages and having a greater effect of mechanical and petrophysical properties, metakaolin is more effective at preventing ASR in lightweight wellbore types of cement containing silica-based microspheres than fly ash.
All of these results also show the importance of testing cement for every job in the conditions that the cement will be used, as everything that changes in the subsurface that might alter the initial cement slurry design can have long term effects on wellbore integrity over the lifecycle of each well.
The authors of this paper would like to thank the members of Dr. Radonjic’s Sustainable Energy & Environmental Research (SEER) Group for their support during this project.
Gratitude to Dr.Clayton Leohn of LSU’s for shared instrument facility and imaging. Appreciation to James Heathman and Darko Kupresan of Shell for advice on the field application aspects of this project. Also, thanks to Dr.Clara Mata of 3M for the donation of microspheres, as well as Halliburton’s cementing lab for donations of cement. Finally, we are grateful to Dr. Mercy Achang, Oklahoma State University, for her feedback and review.
- Pyatina, T., Sugama, T., Moon, J., James, S., “Effect of Tartaric Acid on Hydration of a Sodium-Metasilicate-Activated Blend of Calcium Aluminate Cement and Fly Ash,” Materials , 9(6), 422 (2016); Special Issue Advances in Geopolymers and Alkali- Activated Materials.
- Pyatina, T., and Sugama, T., “Role of Tartaric Acid in Chemical, Mechanical and Self- Healing Behaviors of a Calcium-Aluminate Cement Blend with Fly Ash F under Steam and Alkali Carbonate Environments at 270 °C,” Materials , 10(4), (2017) 342, doi: 10.3390/ma10040342.
- Bello, K., Radonjic, M., “Petrophysical and Microstructural Evaluation Of The Thermal Cycle Loading Effect On Geothermal Wellbore,” Journal of Porous Media, 18(2), (2015); 137-151.
- Radonjic, M., Bello, K., “Experimental Assessment of Cement Integrity under Geopressured Geothermal Reservoir Conditions,” Paper presented at World Geothermal Congress, Melbourne, Australia, (April, 2015).
- Pang, X., Maxson, J. K., Cuello Jimenez, W., Singh, J. P., & Morgan, R. G., “Microscale Characterization of Field and Laboratory Foamed Cement by Use of X-Ray Microcomputed Tomography,” Society of Petroleum Engineers, (2017, May 1), doi: 10.2118/180278-PA.
- Sabin, F.. “Ultra-Lightweight Cement.” CSI Technologies. DOE Final Report (2005).
- Albers, D. and Radonjic, M., “Prevention of Alkali-Silica Reaction (ASR) in Light- Weight Wellbore Cement Comprising Silicate-based Micro-spheres.” Trondheim, Norway (2017).. OMAE2017-62015.
- Tang, S.,Yao, Y. Andrade, C. Li, Z. , “Recent Durability Studies on Concrete Structure.” Cement and Concrete Research, (2015), 78: 143-54.
- Sarfo-Ansah, J., Atiemo, E. , Boakye, K. , Adjei, D. and Adjaottor, A., “Calcined Clay Pozzolan as an Admixture to Mitigate the Alkali-Silica Reaction in Concrete.” Journal of Materials Science and Chemical Engineering, 2, (2014) ;20-26. doi: 10.4236/msce. 2014.25004.
- Leemann, A., Lörtscher L., et al., “Mitigation of ASR by the Use of Li-NO3– Characterization of the Reaction Products.” Cement and Concrete Research, 59 (2014): 73-86.
- Schneider, J. Hasparyk, N. Silva, D. Monteiro, P., “Effect of Lithium Ni-trate on the Alkali- Silica Reaction Gel.” Journal of the American Ceramic Society (2010) 91.10: 3370-374
- Peiliang Shen, Linnu Lu, Wei Chen, Fazhou Wang, Shuguang Hu, “Efficiency of Metakaolin in Steam Cured High Strength Concrete,” Construction and Building Materials 152, (2017):357-366, ISSN 0950-0618, http://dx.doi.org/10.1016/ j.conbuildmat.2017.07.006.
- Robert D. Moser, Amal R. Jayapalan, Victor Y. Garas, Kimberly E. Kurtis, “Assessment of Binary and Ternary Blends of Metakaolin and Class C Fly Ash for Alkali- Silica Reaction Mitigation in Concrete,” Cement and Concrete Research, 40(12), (2010): 1664-1672, ISSN 0008-8846, http://dx.doi.org/10.1016/j.cemconres.2010.08.006.
- Brufatto, C., Cochran, J., Power, L.C.D., El-Zeghaty, S.Z.A.A., Fraboulet, B., Griffin, T., Munk, S., Justus, F., Levine, J., Montgomery, C., Murphy, D., Pfeiffer, J., Pornpoch, T., Rishmani, L.,. “From Mud to Cement E Building Gas Wells.” Schlumb. Oil Field Rev 15, (2003); 62e76.
- Lindgard, J. Andic-Cakir, O. Fernandes, I., Thomas, M., “Alkali-silica Reactions (ASR): Literature Review on Parameters Influencing Laboratory Performance Testing.” Cement and Concrete Research 42 (2011); 223-243.
- Joaquín Liaudat, Ignacio Carol, Carlos M. López, Victor E. Saouma, “ASR Expansions in Concrete Under Triaxial Confinement,” Cement and Concrete Composites 86, (2018); 160-170, ISSN 0958-9465, https://doi.org/10.1016/ j.cemconcomp.2017.10.010.
- Snellings, R. Mertens, G. Elsen, J., “Supplementary Cementitious Materials.” Review in Mineralogy and Geochemistry. 74 (2012): 211-278.
- Lindgård J, Andiç-Çakır Ö, Fernandes I, Rønning, TF, Thomas, MDA. “Alkali–silica reactions (ASR): Literature review on parameters influencing laboratory performance testing.” Cement and Concrete Research. 42(2) (2012): 223-243. ISSN 0008-8846, https://doi.org/ 10.1016/j.cemconres.2011.10.004.